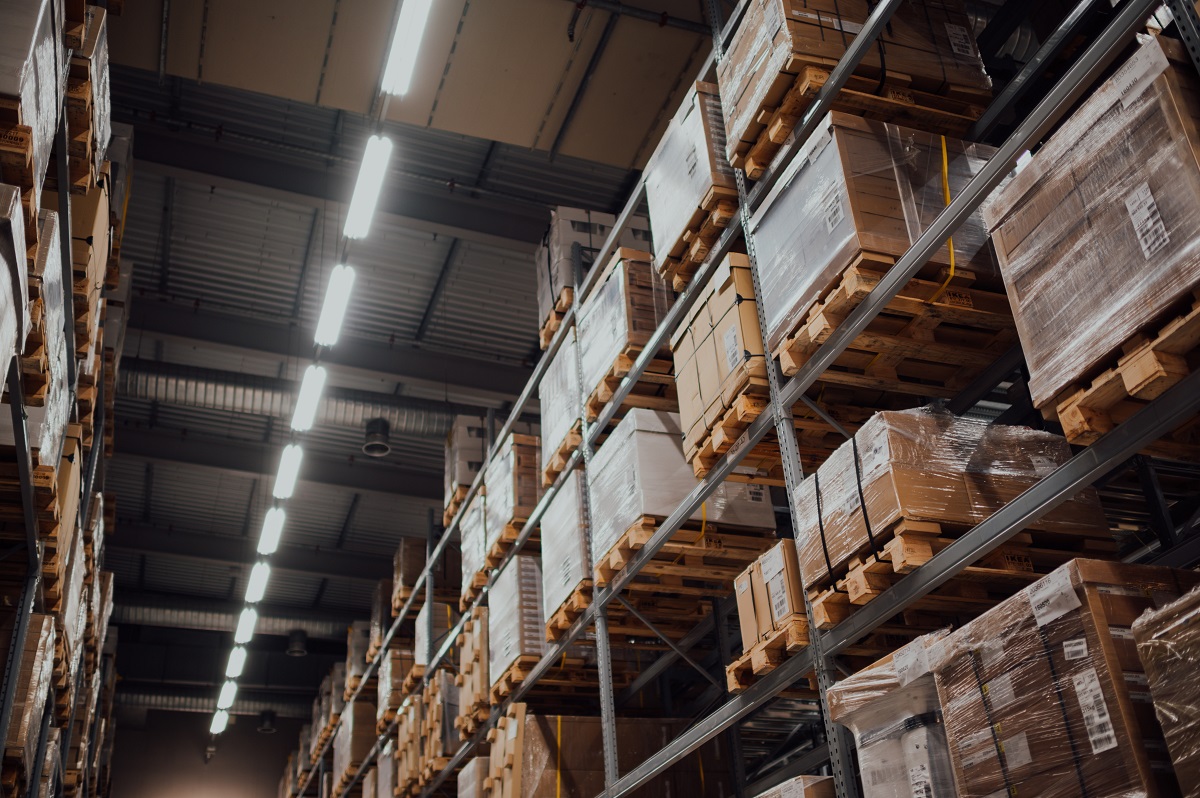
How Streamlining Logistics can Make or Break a Business
January 29, 2021
In order to ensure that operations are running smoothly and efficiently, all businesses should be looking at streamlining their order fulfillment processes. Whether or not your brand is utilising a 3PL warehouse or alternative solutions, streamlining your warehouse processes can dramatically improve efficiency as well as keep costs down.
The warehouse is a critical link in your supply chain, so it is crucial that you take the necessary steps in order to optimise this environment. Below, we’ll run through six tips to help with streamlining warehouse management and logistics.
1. Warehouse Layout and Design
One of the first steps you can take to maximise efficiency in your warehouse space is by making sure the layout and design is optimal for usage. There are a number of reasons why it’s good to make this a priority for your business. Having an efficiently operated warehouse that is safe reduces the risk of injury to employees, speeds up fulfillment of orders as items are easier to locate, can save your business a ton of money and improve overall staff satisfaction.
2. Employee Feedback
Who better to ask about warehouse operations than the people who work in the warehouse? No one will know the ins and outs of processes more than your employees who are working there on a regular basis. Tap into this knowledge and use their expertise to the benefit of your business. They’ll be able to help you recognise where your strengths lie as well as identify any areas of weakness that should be addressed.
3. Labelling and RFID
Every item present in the warehouse should have a label, and you should have a complete labelling plan to compliment this. This will allow staff and management to effectively track everything in the warehouse. In contrast to when things are done manually, it limits the room for error. The use of both barcodes and radio frequency identification (RFID) labels helps keep manual entry of items and products to a minimum. Every shipment that comes in and out of the warehouse needs to be tracked, where this data and information is stored and tracked via warehouse management software (WMS).
4. Delivery Delays
Make sure you keep your customers informed about their order, and this includes if there are any delays. Of course no one likes their items being delayed, but by relaying appropriate information to customers is one simple measure that can build satisfaction amongst your client base. This in turn will lead to more substantial business growth and contented consumers who will remain loyal to your brand.
5. Appropriate Software Solutions
Every business should make sure that they pick software that is appropriate for their specific needs, warehouse space and processes. Your warehouse management software should be able to integrate with other business solutions such as point of sale, ecommerce, fulfillment of orders and inventory management. It’s also handy when your business can seamlessly integrate with your shippers and suppliers.
6. Go Paperless
This is another way to reduce the margin of error, where you will not only save time and money but also have a positive impact on the environment. With the correct warehouse management system, you should be able to generate and view pick & pack lists as well as integrating them onto the devices you use within the warehouse environment. You will also be able to print them, just in case you need a physical copy.
If you take time to implement these tips, you’ll be on your way to streamlining your warehouse logistics and operations in no time. When everything behind the scenes is running smoothly and efficiently, you’ll be able to spend more time on other elements of your business and save money in the long run.